
- Home
- Technology
- Inside Lava's Mobile Manufacturing...
Inside Lava's Mobile Manufacturing Facility: See How Your Smartphone Is Made
The Core visited Lava's manufacturing plant in Noida to understand the stepwise manufacturing of handsets in the unit.
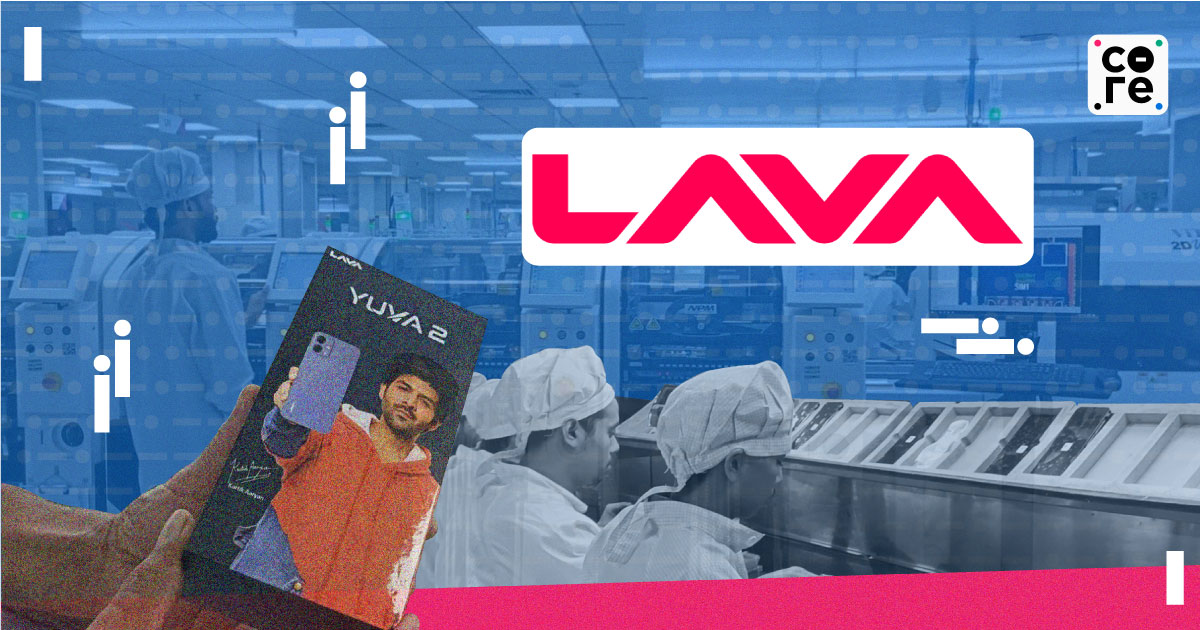
Mobile phones have become an inseparable part of our lives. But have you ever wondered how the device, that you spend hours holding, was actually made? The production process of a mobile phone is an intricate one ? numerous components have to be put together seamlessly to create a functional device. If you look at the process as a whole, it is nothing less than a symphony.
Hundreds of workers collaborate in multiple shifts to put together a smartphone. While most manufacturers are wary of unveiling their manufacturing facilities, Lava opened its doors for The Core to take a guided walk through its shop floor, allowing us to see how the magic happens.
Established in 2009, Indian smartphone manufacturer Lava International Limited was founded by Hari Om Rai, Sunil Bhalla, Shailendra Nath Rai, and Vishal Sehgal. The company is among the leading mobile handset companies in India, with a turnover of over $1.2 billion. Situated in Noida, Uttar Pradesh, Lava?s manufacturing and repair facility where around 3,500 people are involved in the production of 1.5 million feature phones and smartphones monthly.
At a time when the government has pushed the ?Make in India? initiative along with the introduction of a Production Linked Incentive (PLI) Scheme 2.0 for IT Hardware, Lava has taken
Mobile phones have become an inseparable part of our lives. But have you ever wondered how the device, that you spend hours holding, was actually made? The production process of a mobile phone is an intricate one — numerous components have to be put together seamlessly to create a functional device. If you look at the process as a whole, it is nothing less than a symphony.
Hundreds of workers collaborate in multiple shifts to put together a smartphone. While most manufacturers are wary of unveiling their manufacturing facilities, Lava opened its doors for The Core to take a guided walk through its shop floor, allowing us to see how the magic happens.
Established in 2009, Indian smartphone manufacturer Lava International Limited was founded by Hari Om Rai, Sunil Bhalla, Shailendra Nath Rai, and Vishal Sehgal. The company is among the leading mobile handset companies in India, with a turnover of over $1.2 billion. Situated in Noida, Uttar Pradesh, Lava’s manufacturing and repair facility where around 3,500 people are involved in the production of 1.5 million feature phones and smartphones monthly.
At a time when the government has pushed the ‘Make in India’ initiative along with the introduction of a Production Linked Incentive (PLI) Scheme 2.0 for IT Hardware, Lava has taken the lead with a 29% share in ‘Make in India’ shipments in 2022. It was also among the fastest-growing manufacturers in smartphone shipments. India, meanwhile, is set to exceed the Rs 1,20,000 crore mark in mobile phone exports for the ongoing fiscal year, according to the India Cellular and Electronics Association (ICEA), indicating the potential the mobile manufacturing space has.
The Core took an exclusive visit to Lava’s manufacturing plant in sector 63 to understand the stepwise manufacturing of handsets in the unit. We also spoke to Sanjeev Agarwal, Chief Manufacturing Officer on Lava’s future endeavours and strategies.
At present, Lava is manufacturing all its smartphones and feature phones in its Noida facility, which are sold in India as well as sent through exports. “Including feature phones and smartphones, our volume is around 1.5 million per month,” Agarwal told The Core.
“In the near future, we are also planning to start tablets with the introduction of the new policy and we are also looking to do electronic manufacturing services for IT products like laptops, and tablets for other brands as well,” he added.
Lava Assembly Line
We visited the assembly line first, which was meant for assembling and testing. The PCBA i.e. Printed Circuit Board Assembly is done in the SMT (surface-mount technology) facility on a separate floor. We entered the assembly floor through a narrow chamber after undergoing a security check. There were hundreds of workers on the floor who in a synchronised fashion were carrying out individually assigned tasks. Production manager Tilak Budania walked us through the step-by-step assembly process of Lava’s Yuva 2 model on this floor.
First, the raw material for the smartphone is brought to the assembly line on metal trolleys. The assembly begins after the touch panel of the display is inspected.
Next, different parts of the smartphone are assembled together including the side key, camera, receiver and so on.
During the mobile phone assembly process, silica gel is used to protect the electronic components and sensitive parts from heat and moisture.
Then the process of PCBA binding begins. “The PCBA is manufactured by us in the SMT. Specific serial numbers are provided to the PCBs so that tracking becomes easier for any future reference,” Budania said.
Next, the touch panel which was inspected at the start of the assembly line, is assembled with the PCBA.
Approximately 91 people are deployed on one assembly line but the number varies depending on the model and requirement. Around 2,800 smartphones are produced in a shift of eight hours. For feature phones, the number increases to 5200 in terms of production capacity.
The assembled product so far is then passed through a cleaning room. “This is used for those parts which are susceptible to dust particles, like the camera, so that the output is not blurry,” Budania said.
Next, the inner parts are fixed via manual screwing to the PCB before moving to the battery installation step.
During battery installation, the battery is fixed via pressing to avoid any movement and secure it.
/thecore/media/post_attachments/abab3807-952.png)
Two handsets are placed in the machine together to avoid the possibility of battery
blast due to the uneven exerted force.
Then comes the BTB (board-to-board) pressing stage, where the camera and other connectors that were previously fixed, are reverified, so that they are fitted perfectly in their respective positions.
The battery binding process happens adjacently to the BTB pressing stage, where each battery is assigned a serial number. Budania said, “If in case, an issue is encountered then we can easily track the battery and the mobile phone.”
The camera and PCB are covered with a bracket in the subsequent stage manually.
The Auto Screwing Machine (ASM) is among the last steps of assembly, after which the battery cover is placed and the testing starts.
/thecore/media/post_attachments/20690697-7e7.png)
The cover in the ASM has been installed for safety reasons.
On preventive measures taken for the safety of the staff, Budania explained, “Wherever there is a scope of something risky, we provide gloves. Essentially, in smartphones, we don't use any hazardous materials, and even if there is a possibility, safety precautions are built into the machines. There are automatic sensors installed for this purpose. For example, in the ASM a cover is provided so that in case the machine malfunctions or behaves improperly, the cover is there to prevent a battery blast.”
After the final screwing stage, the product passes the cleaning room once again where the film from above the camera is removed and the camera lens is then attached.
The back cover already has adhesive, but the back cover undergoes pressing again for re-verification. The IMEI (International Mobile Equipment Identity) label is also put simultaneously as it contains the complete details of the mobile handset, including the serial number, model colour, and all other specifications.
Highlighting the significance of assembly-focused production, chief manufacturing officer Sanjeev Agarwal said, “Manufacturing is an overall thing. If you are to make a finished product, then the final assembly has to be done. So you have to get all the parts you have to design, you have to source the parts and finally, you have to assemble them and test them and that becomes a product, whether it's an electronics, mobile phone or it's a car, the process is the same. So what we focus is on localization. So how much percentage of parts are localised. Which are developed in India and we are buying locally. For example, in feature phones at present, our localization is 50% of the bill of material value, and in smartphones, it is around 25% of the bill of material value.”
Adding that countries like China are also not doing 100% component manufacturing in China he added, “China is also importing like for example, if you talk about processors, So most of the processors are made in Taiwan or Korea, most of the memories are made in Korea.
So even China imports them. We are also importing. If we talk about smartphones, China is adding around 45-50% value. We are doing value add-on of 25-30%. So there is a gap of 20-25% which I believe we will be able to bridge with the coming benefits and more focus on components and semiconductors.”
Testing Phase
After the assembling is done, functional testing starts for each handset by the product quality and compliance (PQC) department. For inspection, each section has a line leader and the assembly floor has a PQC leader.
To set up a high-functioning manufacturing facility, Agarwal explained that appropriate components, skilled individuals, the right process systems, and a suitable organisational structure are needed. This also necessitates adequate capital investment in plant and machinery, along with strict adherence to the defined process systems to ensure the production of high-quality goods. Similarly, for manufacturing components, capital and advanced technology play a pivotal role in the process.
Before the testing, a dial factory code is inserted so that none of the testing steps are skipped. Until the first test is a success, one isn’t able to move forward with the second one. Explaining the scanning process, Budania said, “Any device that gets rejected in the testing phase, we punch it in our system, i.e. we store its data. It then goes to the repair room, referred to as TRC (Technical Repair Center).”
Next, the earphone testing, SIM and SD card testing is completed, followed by SIM tray insertion.
RF (radio frequency) testing is then conducted to ensure that the device functions effectively when connected to different bits, provided by network operators.
Lastly, visual testing is done for any obvious aesthetic defects.
Testing concludes at this stage, and then we proceed to binning, where sorting of the phones happens based on their model and other specifications. After binning, we moved on to OQA (Overall Quality Assurance) where a 20% sampling is done. Records of the devices that undergo sampling are stored in the database.
The team conducts 100% testing for all the functions in user mode. To ensure the camera does not produce a blurry output, they use colour strips.
In the case of a defect in any device, it is brought to the TRC where the device details are entered into the system. After the repair, the device is set to “repair out”. Until the repair process is completed, the previously dejected device cannot be used in any system.
Next, in the “piggybox stage”, the mobile phone packing is done i.e. the IMEI label is placed outside the gift box, along with the MRP label. The booklet i.e. the user manual with detailed specifications is kept inside each box, which is also binded, to ensure that each box contains one.
The mean weight of a model is previously recorded in the system so that if in the weighing stage, the weight differs, it shows an error.
Lastly, the gift box is wrapped in a shrink pouch, which then goes into a carton box.
Six handsets are placed in one carton. It undergoes a weight check, and if the weight is the same as the one recorded, "SUCCESS” will be displayed on the screen.
Printed Circuit Board Assembly (SMT Manufacturing): Smartphone and Feature Phone Line
After seeing the assembly process, Gaurav Tamta, senior engineer at Lava walked us through the PCBA, which is done in the SMT facility.
The process of PCBA is fairly automated and manual work is done primarily for supervision. First, the production material is brought into the material control room, 24 hours before manufacturing.
PCB assembly involves attaching electronic components to bare PCB boards and then testing them from the user's perspective.
The bare PCBs are loaded on the automatic loader where laser marking is done for future tracking and identification in case of any defects.
Post marking, the PCB undergoes an automated solder paste printing machine, where there is a pre-set customised SMT stencil, that cleans the solder paste in areas where components need to be placed.
The next stage is SPI, Solder Paste Inspection, which checks whether the solder paste is present in the required locations. An operator on-site verifies its accuracy. Once the paste is applied, the components are placed on top. This is the mounting process, starting with small components and then larger ones.
AOI (Automatic Optical Inspection) verifies whether the components have been correctly placed as per the desired specifications.
Next, a metallic shield is applied for the safety of the components.
Now that the mounting process is complete, the next step is reflow. In reflow, a joint is created between the component and the PCB, primarily through the melting of solder paste.
Lastly, the PCB panel is cut into separate individual pieces and sent for testing.
PCB Testing
In the testing phase, the first step involves loading software onto the PCB since the PCB is empty.
/thecore/media/post_attachments/7305d9f3-dcd.png)
RF Calibration is performed to assess calling capability. It involves creating a structure similar to the external environment and setting the radio frequency to capture the phone network's range.
Next, the PCB is put through MMI (Man-Machine Interface) testing. This involves manual testing with a dummy device, simulating the same actions as we would with a phone.
Lastly, the water labelling process, designed to protect against water damage followed by visual inspection, is done, post which the PCB is sent to the assembly floor.
Way Forward
At present, the Lava manufacturing facility in Noida has a 40% extra cap and is the company’s only facility in the country. “Once the need arises for more facilities, then we will go for it,” Agarwal said.
As Lava aims to manufacture tablets and laptops in the future, Agarwal said that the focus should come on components now. “With the new PLI definitely, in one or two years time, there will be a lot of local manufacturing which will start. But for mobile phones, the focus should be now on components, and how to have more localisation of components that will bring more value additions,” Agarwal said.
“The main focus should be on productivity because when a country grows, then labour costs will increase. Because if our GDP increases, then people’s salaries have to go up, which has already happened in China. So that will definitely happen in India also. But we have to improve our productivity with the same people, how we can produce more, do more, that is more important,” he added.
ALSO READ: Post-Covid Recovery, EV Interest: Why 3-Wheeler Sales Are Zooming Ahead
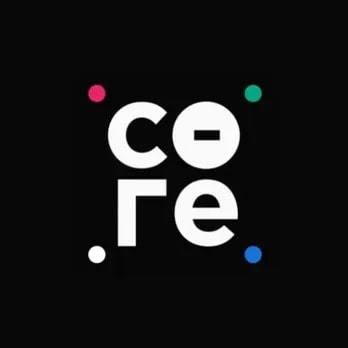
The Core visited Lava's manufacturing plant in Noida to understand the stepwise manufacturing of handsets in the unit.