
On The Shopfloor: A Day At Greenfuel Energy Solutions' EV Battery Plant
The Core visited Greenfuel's Manesar plant to understand how a lithium-ion battery pack for electric vehicles is made.
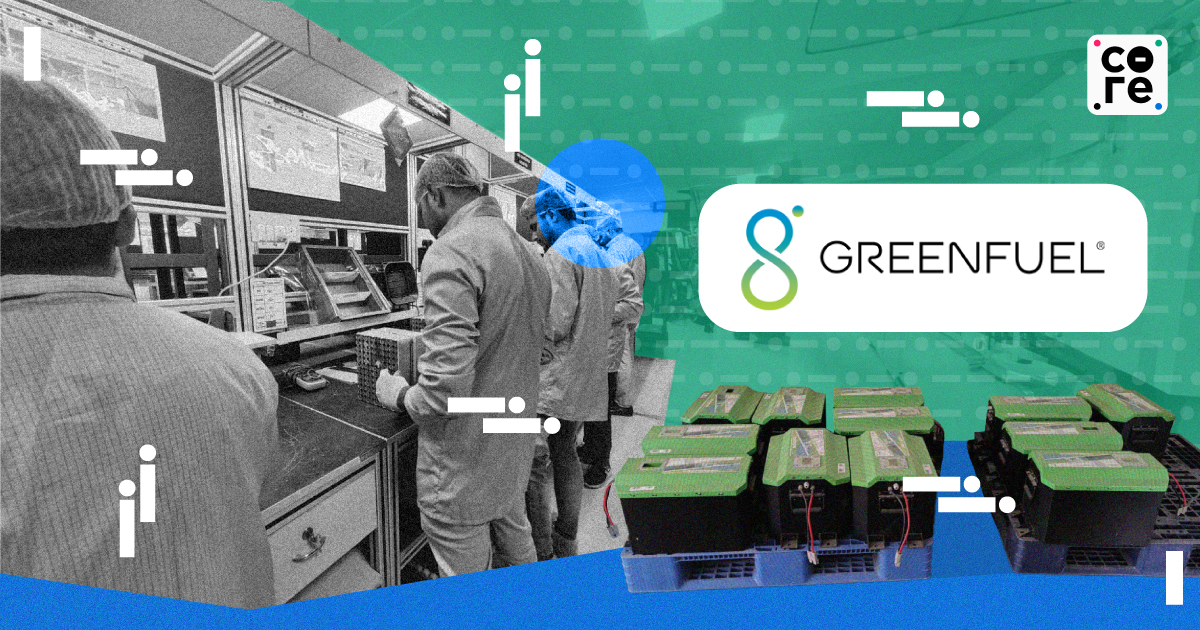
Have you ever wondered what goes into the making of the battery that powers your electric vehicle (EV)? EVs are the talk of the town now and its claim as a sustainability-friendly alternative is powered by a rechargeable battery. While that is by and large known to everyone, what you might not have known is how this battery is made.
Manesar, about 60 kilometres south of India's capital city New Delhi, is one of the leading automobile hubs of India. In a wide, leafy lane here, situated amid a cluster of other automotive manufacturing units, is the battery plant of Greenfuel Energy Solutions. The company has about 28 workers on two assembly lines to make EV batteries.
The Beginnings
Founded in 2006, Greenfuel Energy Solutions has always been geared towards clean mobility solutions. It started operations with the aim of providing solutions for compressed natural gas (CNG) systems across various vehicles. Since 2011, the company has been looking at e-mobility as a natural progression towards the clean mobility landscape, the company?s founder and managing director Akshay Kashyap told The Core.
The company currently has a market share of 40% in EV batteries for e-rickshaws and 10% for two-wheelers. They have four patents for battery packs as well. There is huge potential for the EV battery market in India. According to a report by GameChanger Law Advisors and Speciale Invest, the Indian EV battery market w...
Have you ever wondered what goes into the making of the battery that powers your electric vehicle (EV)? EVs are the talk of the town now and its claim as a sustainability-friendly alternative is powered by a rechargeable battery. While that is by and large known to everyone, what you might not have known is how this battery is made.
Manesar, about 60 kilometres south of India's capital city New Delhi, is one of the leading automobile hubs of India. In a wide, leafy lane here, situated amid a cluster of other automotive manufacturing units, is the battery plant of Greenfuel Energy Solutions. The company has about 28 workers on two assembly lines to make EV batteries.
The Beginnings
Founded in 2006, Greenfuel Energy Solutions has always been geared towards clean mobility solutions. It started operations with the aim of providing solutions for compressed natural gas (CNG) systems across various vehicles. Since 2011, the company has been looking at e-mobility as a natural progression towards the clean mobility landscape, the company’s founder and managing director Akshay Kashyap told The Core.
The company currently has a market share of 40% in EV batteries for e-rickshaws and 10% for two-wheelers. They have four patents for battery packs as well. There is huge potential for the EV battery market in India. According to a report by GameChanger Law Advisors and Speciale Invest, the Indian EV battery market will grow from US $16.77 billion in 2023 to US $27.70 billion by 2028, with a compound annual growth rate of 10.56% in 2023-2028.
In 2016, they decided to take the plunge. “What we did was, we hired an expert from Sweden and built a core team around him to build battery packs for the Indian market,” Kashyap said. The company spent two and a half years on research and development to ensure the lithium ion batteries were reliable, safe and well-suited for the Indian tropical climate and were geared towards creating a zero defect product.
The Core visited Greenfuel’s Manesar plant to understand how a lithium-ion battery pack for electric vehicles is made.
Understanding The Process
Greenfuel manufactures two kinds of lithium-ion battery packs used in EVs – the cylindrical or nickel manganese cobalt (NMC) batteries which are used in two-wheelers, as well as prismatic or lithium iron phosphate (LFP) batteries, used in three-wheelers and four-wheelers.
A lithium-ion battery pack is made by connecting several individual lithium ion battery cells. A battery cell is the foundation – it charges and discharges electric current through the flow of lithium ions moving between the negative (anode) and positive (cathode) electrodes.
Greenfuel makes both 48 volt and 72 volt LFP battery packs. In a day, the company manufactures about 50 packs.
The company first tests the capacity of the cells imported from China. Simply put, cell capacity is the amount of constant electricity drawn from the cell at a particular rate of discharge until it drains out in a given time. It is measured in ampere-hours (mAh), and the higher the rating, the longer the battery will last.
While the other components used by the company are all made in India, there is still a lack of indigenous cell makers in the country. “Validation of a cell is very important especially when you buy Chinese cells. So we have a 4-5 months very stringent validation process,” said Kashyap.
Individual cells are tested for voltage range, and internal resistance (IR) range in cell capacity testing machines, a process which takes about six hours, Nitin Mohil, manager, production at Greenfuel told The Core.
Since there can be minor differences in the voltage and IR of each cell, these are recorded, and the capacity can range anywhere between 3200 mAh to 3400 mAh.
Gradation And Packaging
Based on this range, Greenfuel divides the cells into different grades, ranging from A1 to D20. The sorting process is also mechanised. The cells used in a battery pack need to have the same grade for optimum performance, Noneet Singh, senior engineer, quality assurance, explained.
The cells, packed according to their individual grades, are then taken to the assembly line. Here, insulating paper is pasted on the positive electrode of the cell. Barley paper stickers are used for this, because they have good insulation and wear resistance. This is done to prevent short circuits of the battery pack during vibration.
After this, the cells are assembled in holders. This is done in a combination of series (columns) and parallels (rows). A 48 volt NMC battery has 14 series and 12 parallels, meaning the cells in the pack are arranged in a combination of 14 x 12.
The cells are then connected by nickel holders, manually.
The next step is spot welding, done automatically. A machine uses heat to connect the contact point, or terminal, of the cells to the nickel holders. A worker then manually tests whether the welding is strong enough to hold the connection.
The sorting of cells into grades is tested again. The IR of each series is tested by a machine. For each, there can be a maximum difference of 10 millivolt and 50 milliohm. Anything more than this would indicate that battery cells used in that particular pack are not of the same grade. This hasn’t happened yet, Mohil said, but if it were to happen, the cells would be taken back for capacity testing.
Temperature Evaluation
Temperature testing is done after this, where temperature sensors are taped to the battery pack. This is later attached to the Battery Management System (BMS), also known as the brain of the pack. It monitors the temperature, and if it goes above 55 degree celsius when the battery is being used – either charging or discharging electricity – the battery pack will go into protection mode, and essentially stop. This helps prevent overheating of the battery.
While the ideal temperature of a battery pack is supposed to be 28 degrees, it can increase during usage, and so monitoring it through the BMS is important.
Each series is then connected to a cable via soldering to monitor voltage and the cables are routed in a spiral sleeve.
The pack is then wrapped in yellow epoxy – this is a FRP plastic cover with a high melting point to protect the pack against short circuits.
Understanding BMS
The BMS, which monitors the battery's performance, is finally soldered and attached to the pack.
After the BMS is added, the pack is inserted in a metal bracket and closed.
The last chapter involves testing of each battery pack. This process is mechanised, and called ‘ageing’. The packs are connected to testing machines, which ensure that all the metrics of the battery, including the voltage, temperature, and current are up to code. This is done by a repeating cycle of charging the battery, putting it in discharging mode (drawing power from it), and putting it in rest mode.
Kashyap pointed out that it is important for customers to understand the difference between a designed battery pack and an assembled one. “The industry is still at a nascent stage where even the end user doesn't understand the difference between a reliable performing product versus a Chinese assembled product,” he said. Finding the right skilled workers is another challenge, he added.
However, with larger original equipment manufacturers (OEMs) entering the EV market, the company is optimistic about standards changing. “As the traditional OEMs are getting into the business…their demands are much more stringent, much more technical and therefore players like us have a very good time now,” he said.
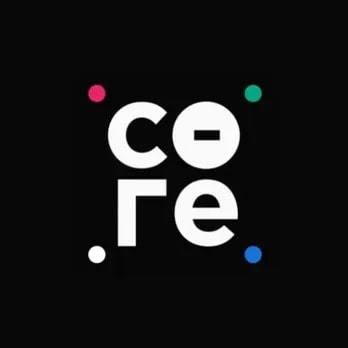
The Core visited Greenfuel's Manesar plant to understand how a lithium-ion battery pack for electric vehicles is made.